BACKGROUND
In the evolving landscape of telecommunications, the need for smaller fibre optic cables and ducts in Europe is becoming increasingly apparent. This necessity is driven by a multitude of factors, ranging from technological advancements to practical considerations in urban planning, installation time and costs, and infrastructure management.
A key reason for the push towards smaller fibre optic cables and ducts is the congestion of underground space. European cities often have extensive utility networks, including for water, gas, electricity, and telecommunications, all competing for limited space.
HFCL, a leading manufacturer of telecommunication equipment and fibre optic cables in India, was appointed to design and manufacture fibre optic cables that offer a smaller footprint but also enhanced performance in the United Kingdom.
To meet the requirements of the demanding telecommunications industry, HFCL had to create a cable with an ultra-thin fibre optic cable jacket.
To meet the growing demands of high-speed data transmission and efficient network deployment, HFCL designed a closed fibre unit (CFU), that incorporates modern materials and advance design principles.
HFCL worked closely with Borouge and Borealis,to develop an innovative solution to address the project needs. The development of the CFU cable had presented several challenges:
- Minimise surface contact between the duct and cable jacket to enhance installation efficiency
- Ensure cable can withstand rigours of being blown over distances of up to 1 kilometre through a 5/3.5mm duct while maintaining mechanical integrity
- Ensure the fibre optic cores maintained low attenuation and high performance
SOLUTION
The cornerstone of HFCL’s innovative solution lies in the use of Borstar® HE6067. The material is a black high-density polyethylene (HDPE) material with exceptionally low shrinkage properties.
Material Excellence: Borstar® HE6067’s low shrinkage properties enabled the creation of a cable jacket measuring between 0.10mm to 0.15mm, significantly reducing the cable’s footprint while ensuring robustness against the stresses of installation with exceptional tear resistance.
Innovative Design: The CFU cable features multiple fibre optic cores, protected by a low friction outer sheath. The use of G.657A1 reliable high-performance single mode fibres with low attenuation further improves the cable’s bending properties and overall performance.
IMPACT
The CFU cable’s design is transforming the telecommunications industry by offering a more efficient and sustainable solution. Key impacts include:
Technological Advancement: The smaller, more compact design allows for higher data transmission speeds and greater capacities, while optimising space and reducing environmental footprint.
Cost-Effectiveness: The reduced size and material usage lower production, transportation, and carbon emissions costs, making the deployment of smaller ducts more economical.
Sustainability: The reduction in material usage and smaller excavation footprints help preserve natural resources and reduce the carbon emissions
General Manager R&D of HFCL, Mr. Stanley Chand, expressed his satisfaction with the development, highlighting that the innovative CFU cable offers superior installation and blowing performance while contributing to environmental sustainability. He stated, “This project is a testament to our commitment to innovation and excellence, and our vision to be a leading fibre optic cable manufacturer in India and beyond.”
This successful implementation of the Borstar® HE6067 for micro-cable designs exemplifies the dedication to pushing the boundaries of fibre optic cable technology, setting new industry standards, and fostering sustainability through advanced materials and innovative design.
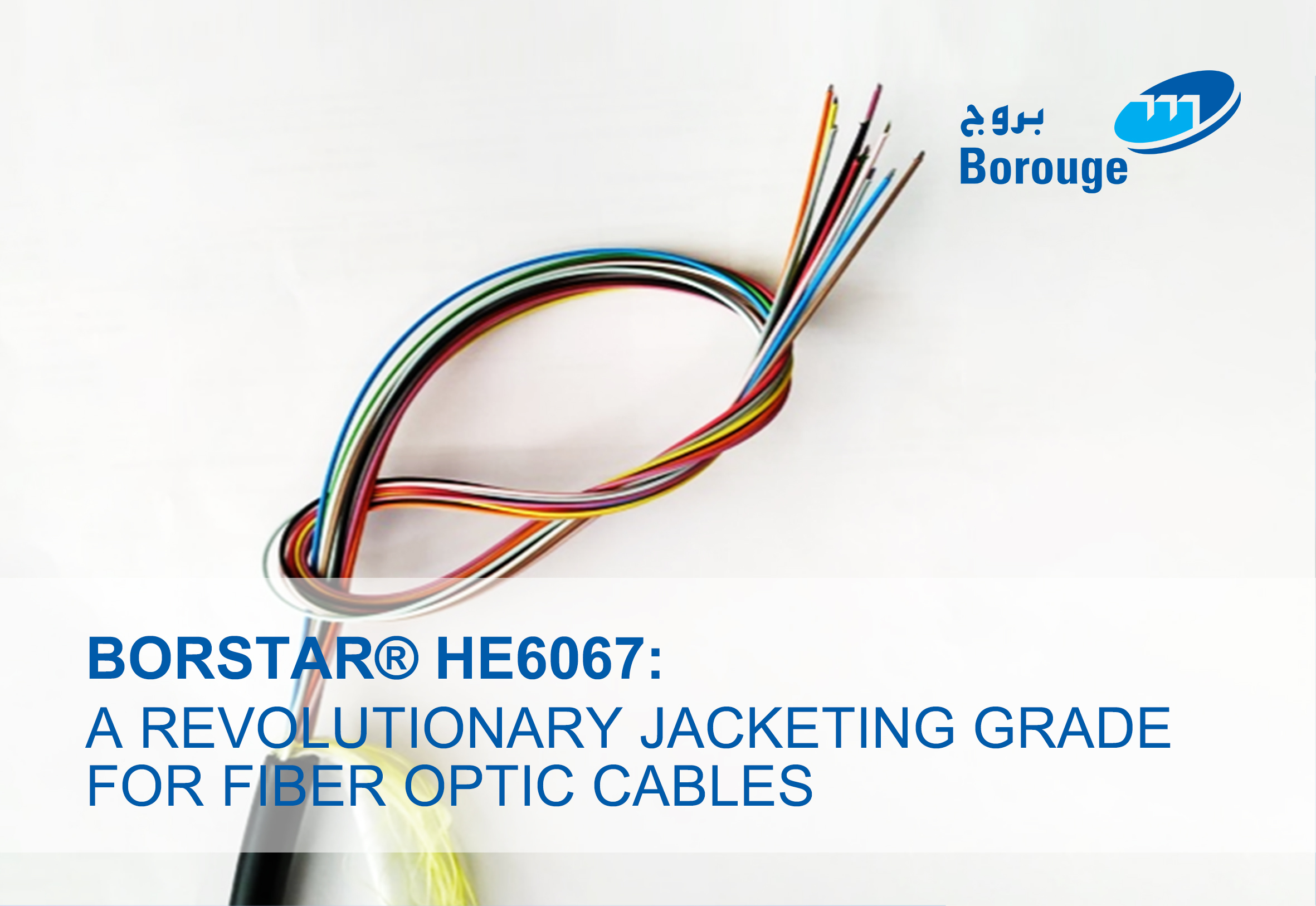